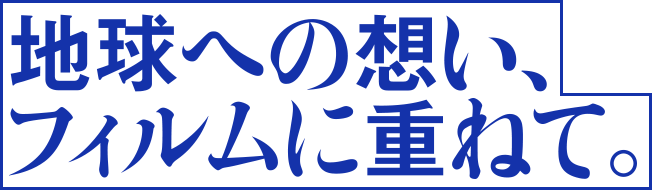
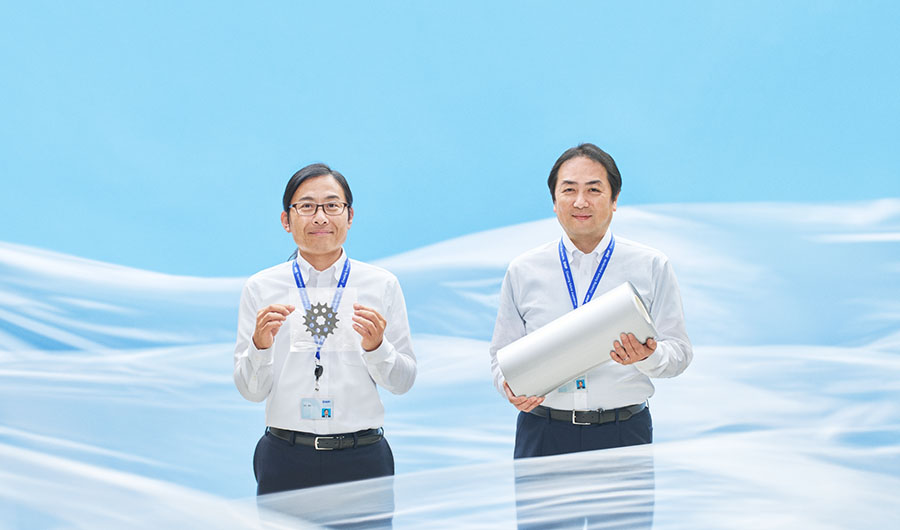
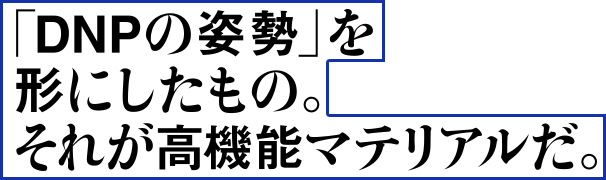
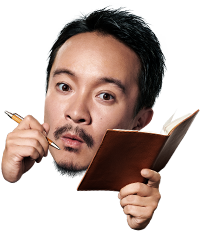
「高機能マテリアル」とは何か? それはDNPがずっと大切にし続けてきた“社会に対する姿勢”を表したものともいえる。直訳すると「高機能な原材料・素材」。だが、DNPの「高機能マテリアル」はその範疇に収まらない。
まだ世の中にない「あったらいいな」「あるべきだ」に耳を傾け、新たなマーケットを創出してきたDNPの歴史――。その成果のひとつ、1990年代から開発を続けてきた高機能なフィルム製品について、高機能マテリアル事業部の浜田正道と石川裕之に話を聞いた。
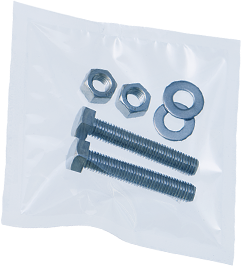
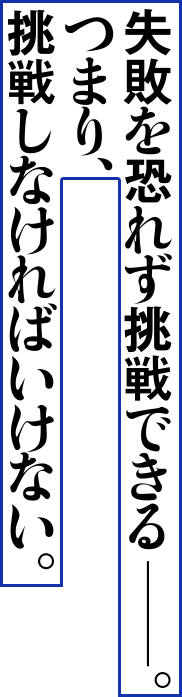
高機能マテリアル事業部でともに働く浜田と石川。浜田はバッテリーパウチ、石川は 防錆性 フィルムを担当している。まず二人にDNPに入社したきっかけや会社の印象などを聞いた。
“大学の研究室の先輩がDNPに入社していていろいろと話を聞けたことに加え、DNPが非常に社会貢献性の高い事業をおこなっていたことも理由のひとつ。最終的に背中を押してくれたのは、「やりがいしかない、楽しいぞ」という先輩の言葉でした。(浜田)”
“私は、大学のときと同じ研究をおこなっている部署がDNPにあり、その評価研究ができたらいいなと考えて入社しました。DNPの奥の深さは、入社してみてはじめて気づいた、というのが実際のところです。(石川)”
浜田は27年、石川は22年にわたって、DNPで仕事をしている。
“DNPの一番の魅力は、やりたいことをやらせてくれるところ。どんな仕事にも失敗はつきもので、特に新しいことへの挑戦ならなおさら。でも、その失敗を失敗で終わらせないフォローや体制がある。だからこそ、もちろん責任をともないますが、自由に仕事を進めることもできる。それは、まさに社風ですね。(浜田)”
“最初は大学での研究とは異なる分野に取り組むことになりました。思い返してみると、その経験で、技術や研究・開発への視野は確実に広がった。ある課題へのソリューションに至るアプローチは決してひとつじゃない。DNPの持つ開発分野の裾野の広さにも気づけましたね。(石川)”
そして二人は現在、高機能マテリアル事業部で製品の開発と営業に携わっている。そこにある挑戦とは、その先にある「未来のあたりまえ」とは、どんな姿をしているのか。
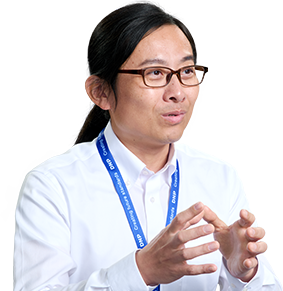
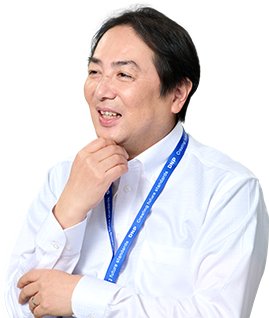
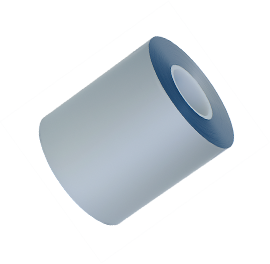
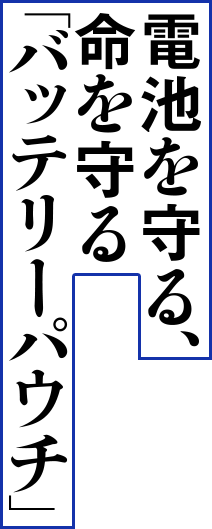
バッテリーパウチ。それはひと言で表すと「リチウムイオン電池の外装材」である。リチウムイオン電池は、内部に液体電解質を含んでおり、外部からの衝撃や圧力に弱い。外装材はこれらの衝撃から電池本体を保護し、内部の構造を安定させる役割がある。主に電子機器や電気自動車に使われており、一般にも馴染み深い乾電池をはじめとする金属缶のバッテリーとの最大の違いは「フレキシブル性」だ。
“バッテリーパウチは、フィルムタイプの外装材です。カレーなどのレトルトパウチを想像していただくとイメージしやすいかもしれません。金属缶のバッテリーはサイズが決まっているので、それを考慮した設計が必要ですが、バッテリーパウチは、大きさや形状をある程度自由に変えられるため、自動車のデザインを優先して車体に組み込むことができるのも、大きな強みのひとつです。(浜田)”
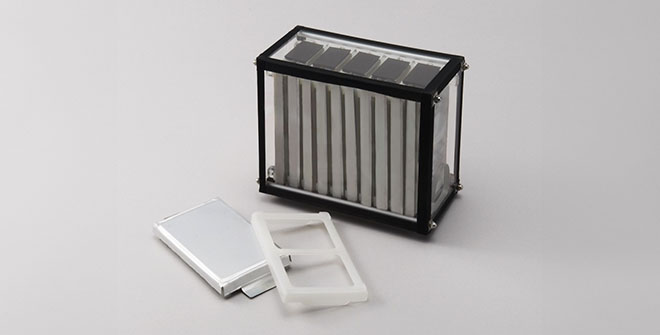
DNPがバッテリーパウチの開発を始めたのは1992年。研究・開発に14年間の時間を要し、その間、売上にはつながらなかった。しかし、2006年に潮目が変わる。ある自動車メーカーが研究車両を製作し、電力会社と共同研究を進めることを発表。現在へと続く電気自動車の開発が本格的にスタートしたのだ。この時期を境として、バッテリーパウチへの需要は高まっていく。
“それから現在に至るまで、我々はバッテリーパウチの進化を支えてきました。たとえば、発売当初の電気自動車に搭載されていた電池を分解して、性能が劣化していないかどうか、劣化しているとすればどの程度なのかなども、常にチェックを続けています。まだ社会で広く注目されていない頃から、未来を見据えて研究・開発を続けてきたからこそ、現在私たちのバッテリーパウチを選んでいただける結果になっているのだと思います。正に「未来のあたりまえ」を実現した製品なのです。(浜田)”
そう語る浜田の視線は、すでに次世代型の電池を見据えている。そこには変化する社会ニーズや、自動車メーカーが抱える課題も関係している。
“私たちの直接的なお客様は電池メーカーです。ただ、それを自動車に実装して生活者の皆さんに届ける自動車メーカーともお話をさせていただいています。その結果、「人を運ぶモビリティ」について大きな責務と課題、具体的に言えば「自動車の安全性能」をより深掘りして考える必要性も実感できるんです。次世代型の「全固体電池」に対する期待も、肌で感じています。(浜田)”
この「全固体電池」は、電池の内部に液体電解質を使わず、固体電解質を使用するものだが、その特徴は大きくふたつある。ひとつは、充電・放電の時間が短いこと。現在、30分〜1時間かかる電気自動車の充電を、約10分でできる可能性を秘めている。そしてもうひとつは、現状よりもさらに高い安全性。発火しにくいという特性があり、例えば300℃という高温にも耐えられると言われている。
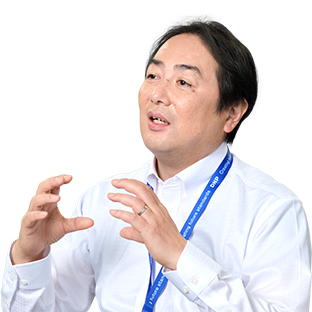
“全固体電池を作るためには、内部の固体電解質と正極・負極の密着が非常に重要です。密着をさせるために圧をかける必要がある。フィルムのフレキシブル性がここでも必要となってくる。つまり、近い将来、全固体電池が世の中に流通していくには、バッテリーパウチの必要性はさらに高まると考えています。現状のフィルム機能に満足しているわけにはいかない。世の中の変化を眺めるのではなく、さらにより良いものにしていくにはどうしたらいいか?さらに社会に貢献できる高機能が付加されたフィルムとは何か?それを先取りして考え続けています。(浜田)”
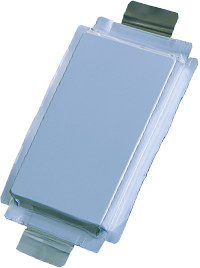
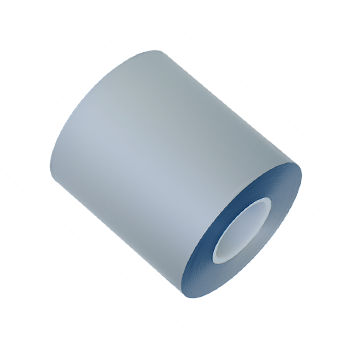
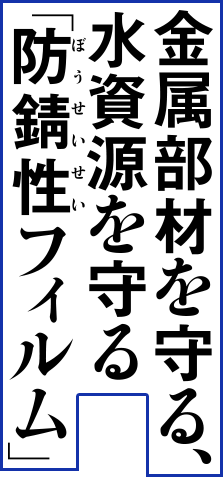
さかのぼれば人類は、鉄の利用の拡大とともに「錆」を防ぐ戦いを続け、その過程でさまざまな技術を生み出してきた。そしてその延長線上に、DNPも「防錆性フィルム」を誕生させた。この製品は薄いガラス膜を付加することで、水や酸素といった錆の原因をバリアするフィルムである。
“現在でも、錆を抑制するためにさまざまなものが使われています。シリカゲルのように水分を吸着するものだったり、また錆を防止する成分がにじみ出る気化性防錆フィルムを用いたり。ただ、空気中には酸素も水分もありますから、常に錆が発生する条件は整っているのです。DNP防錆性フィルムは、「水分バリア機能」、「酸素バリア機能」、「衝撃バリア機能」という3つの機能を備え、錆の発生原因と触れる量を極力減少させるという考え方で開発したものです。(石川)”
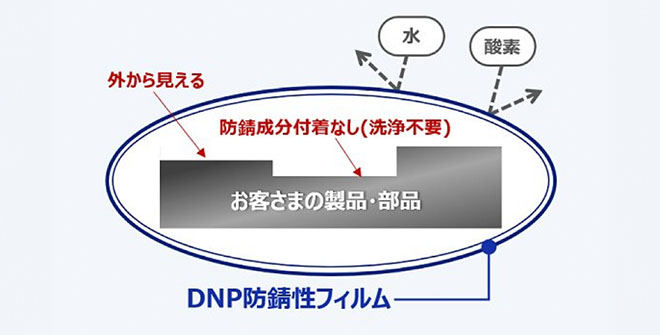
DNPの防錆性フィルムにはもうひとつ大きな特徴がある。それは「透明」であるということ。例えば輸出入時の通関を想像してほしい。先述した通り、物質は空気に触れた瞬間に、錆の発生条件が整ってしまう。つまり厳重に防錆保管をしたとしても、透明ではないために中身の確認にフィルムを開けられてしまったら、元も子もないのだ。
“加えて、DNPの「防錆性フィルム」が選ばれる大きな理由のひとつに、「環境保全」へのメリットが挙げられます。錆を発生させない手法として、例えば防錆油を塗布した場合、最終的にその防錆油を落とさなければならない。その際に、大量の水資源が必要となります。さらに塗布した防錆油も、水と一緒に流れていってしまう。また、シリカゲルは日本では産廃としての処分が必要です。フィルムそのもので錆を防げば、環境負荷を減らすことができるんです。(石川)”
特に水資源が乏しい国・地域にとっては、大量の水の使用を前提とする手法は、産業振興のボトルネックとなる。だからこそ、製品自体、例えばフィルムそのものが錆を防ぐ機能を持つことの意味が高くなる。製品が水資源を守り、ひいては環境負荷の減少に直結するという視点で見たとき、予想以上に高機能マテリアル事業の奥が深く、その提供価値が高いことがわかる。
“ある産業が必要とする機能をフィルムの形で提供する。それだけでなく、地球環境も見据えてフィルム製品を開発し、社会に実装させていく。それがDNPの高機能マテリアル事業が目指すところです。目には見えない機能を多層化したフィルムで実現できる領域は広く、未来ではさらに拡張していけると考えています。(石川)”
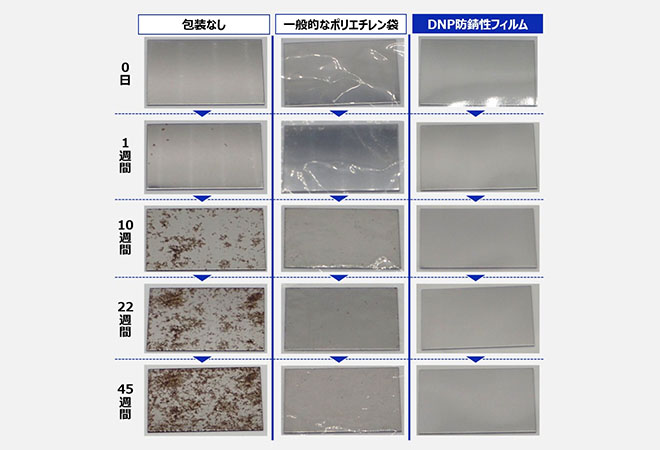
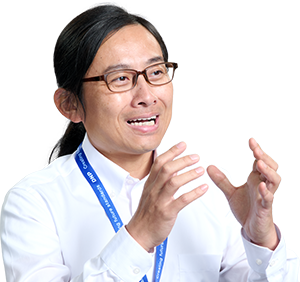
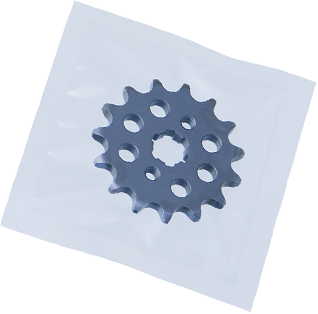
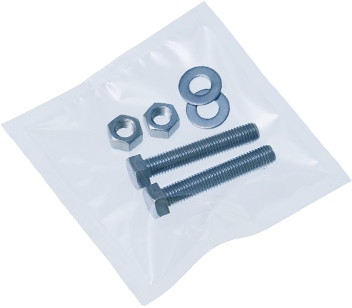
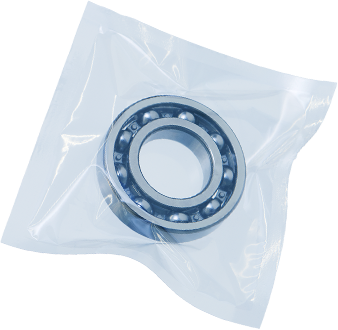

現在、高機能マテリアル関連の事業では主に、「バッテリーパウチ」「防錆性フィルム」「バリアフィルム」「太陽光パネル関連部材」の研究・開発と、製品化を進めている。例えば、「太陽光パネル関連部材」についても、世界で重要な立ち位置を占めている。
“より発電効率が良く、より環境負荷の少ない次世代型の太陽光パネル関連部材の可能性も探っています。常に世の中にないものを生み出し、それを社会実装させてきたDNPとして、可能性を追い続けるのは「あたりまえ」のことなんです。近い未来には、フィルムという形すらも変わっている可能性はあります。それも、おもしろいですよね。(浜田)”
世の中にないものをつくる。そして、それを社会に普及させ、みんなの「あたりまえ」にする。バッテリーパウチも防錆性フィルムも、10年単位の開発の歴史を積み重ねている。未来を想像しながら仕事していくことは、DNPにとって「通常運転」なのだ。
“最初にバッテリーパウチのアイデアを出した社員は、本当にクルマが好きな人でした。自動車メーカーなどで行っている走行テストのライセンスを持っていたくらいの人です。電気で走る車に乗ってみたい!それがあたりまえの未来を生きてみたい!そんな初動の思いを語り、仲間たちを巻き込み、突き動かし、年月をかけて技術を刷新・洗練させていく。今ここにある製品・サービスは、そういった思いの結晶であるとも言えるんです。(浜田)”
“金属は、いつか錆びる。では錆びるまでの時間をどこまで長くできるか。たとえば産業機器やクルマなどを持続可能にするため、今使っている機械や部品を未来に残さなければならないという業界ニーズが必ずあるわけです。10年や20年といったスパンでそれを保存する際に、我々の「防錆性フィルム」は必ず役に立つ。「今」と「未来」をつなげていく機能が、この製品には含まれているんですよ。(石川)”
「何かを守る」ことを求められ、製品化してきた高機能マテリアル事業部。金属を錆から「守る」ため、水資源を「守る」ため、安全性を向上させて人の命を「守る」ため。それが巡り巡って地球の未来を「守る」ため、へとつながっていく。フィルムという一見何の変哲もないマテリアルが注目され始めているのは、まさにそこに今「未来のあたりまえ」がつくり出されようとしているダイナミズムがあるからだ。
“今後さらに人類の普遍的な要求を可視化して、いわば「“世界”の、未来のあたりまえ」をつくることがDNPに求められていくはずです。地球環境や安全への対応など、すべての産業で要求水準が高まっていますが、これは社会の必然的な要請だと思います。間違いなくこの先、もっともっと守らなければいけないものが出てくるはずだし、守れるものも増えていくはず。そのときに私たちに何ができるかを考えていると、時間はいくらあっても足りませんね(笑)。(浜田)”
“社内の研修で、「日本にいると、1日中DNPの製品・サービスに触れずに生活することは不可能だ」という話を聞いたことがあります。それくらい我々の製品・サービスは生活の中に入り込んでいる。それは一方で、より社会に対して責任を果たす必要があるということ。我々の部署のミッションは「中身を“守る”」マテリアルの開発~普及ですが、そこに別の価値を付加していくことが重要だと思います。目の前にあるものだけではなく、その先で必要になる何かにまでフォーカスし、機能を高めていかないといけません。「見えないものまで守る」ことができる仕事って、すごく楽しそうだと思いません?(石川)”
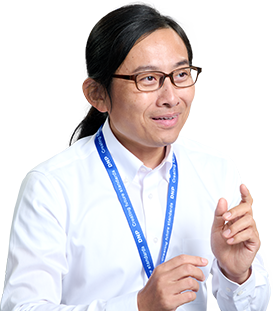
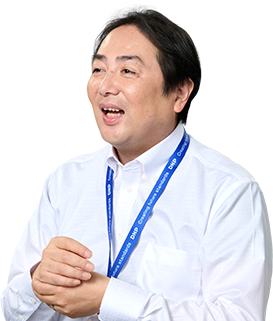
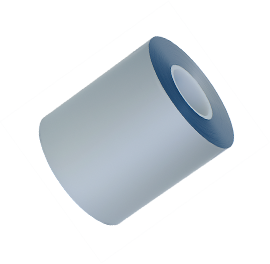

2025年02月公開